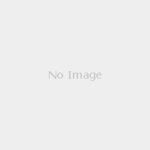
Product Categories
- Agriculture
-
- Agriculture & By-product Agents
- Agriculture Product Stocks
- Agrochemicals & Pesticides
- Animal Extract
- Animal Fodders
- Animal Husbandry
- Bamboo & Rattan Products
- Beans
- Cigarette & Tobacco
- Eggs
- Farm Machines & Tools
- Fishery Machinery
- Flowers & Plant
- Forest Machinery
- Fruit
- Grain
- Mushroom & Truffle
- Nuts & Kernels
- Others
- Plant & Animal Oil
- Plant Extract
- Plant Seed
- Poultry & Livestock
- Vegetable
-
- Apparel & Fashion
-
- Used Clothes
- Uniforms & Workwear
- Underwear & Nightwear
- Swimwear & Beachwear
- T-Shirts
- Sweaters
- Apparel & Fashion Agents
- Apparel Stocks
- Athletic Wear
- Bathrobe
- Children Garment
- Costume & Ceremony
- Down Garment
- Ethnic Garment
- Fashion Accessories
- Footwear
- Fur Garment
- Garment Accessories
- Gloves & Mittens
- Infant Garment
- Jacket
- Jeans
- Leather Garment
- Leisure Wear
- Others
- Outerwear
- Pants & Trousers
- Related Machine
- Sewing Machinery
- Shirts & Blouses
- Silk Garment
- Skirts & Dresses
- Socks & Stockings
- Speciality
- Suits & Tuxedo
-
- Automobile
-
- Auto Electrical System
- Auto Accessories
- Auto Electronics
- Auto Maintenance
- Auto Parts
- Auto Production Line Equipment
- Automobile
- Automobile & Parts Agent
- Automobile Stocks
- Electric Motorcycles
- Motorcycle Accessories
- Motorcycle Parts
- Motorcycles
- Others
- Parking
- Second Hand
- Special Transportation Equipment
-
- Business Services
-
- Advertising
- Auction
- Brokerage, Intermediary Services
- Cargo & Storage
- Commercial Service
- Consulting
- Designing, Processing, Custom Made
- Economic Cooperation
- Education & Training
- Exhibitions & Fairs
- Funeral & Interment
- General Trade Agents
- Inspection & Quality Control Services
- Labor & Employment
- Legal, Public Notary Services
- Others
- Packaging & Printing Service
- Passport & Visa
- Pawn, Leasing
- Regional Trade Agents
- Repairing
- Retailing
- Service Agent
- Service Equipment & Supplies
- Telecommunication & Postal Services
- Therapies
- Translation Services
- Travel
- Wedding & Ceremony
-
- Chemicals
-
- Activated Carbon
- Adhesives & Sealants
- Catalysts
- Chemical Additives, Auxiliary
- Chemical Machinery
- Chemical Reagent
- Chemicals Agents
- Chemicals Stocks
- Coatings
- Dyestuffs
- Explosive
- Fine Chemicals
- Fodder, Feed Additives
- Food Additives
- High Polymers
- Inorganic Chemical Materials
- Lab Supplies
- Organic Chemical Materials
- Others
- Paint
- Pigment
- Plastics & Products
- Printing Oil
- Resin
- Rubber & Products
-
- Computer Hardware & Software
- Construction & Real Estate
-
- Adhesives
- Bath & Toilet Appliances
- Bricks & Pavers
- Building Ceramic
- Building Coating
- Building Facilities
- Building Glass
- Building Metallic Materials
- Building Plastic
- Cement & Sand
- Construction Hardware
- Construction Machinery
- Construction Materials Agents
- Construction Materials Stocks
- Decorative Materials
- Doorbells
- Doors & Windows
- Earthwork Products
- Fireproof Materials
- Flooring & Tiles
- Heat Insulation
- Kitchen Appliances
- Lime & Plaster
- Others
- Pipe & Fittings
- Real Estate
- Real Estate Agents
- Soundproof Materials
- Special Materials
- Stone, Marble
- Timber & Plank
- Wall Materials
- Wallpaper
- Waterproof Materials
-
- Electronics & Electrical
-
- Batteries & Chargers
- Capacitors
- Chargers
- Circuit Breaker
- Commercial Field
- Contactor
- EL Products
- Electric Power Tools
- Electrical Outlets & Plugs
- Electrical Product Agent
- Electronic Component
- Electronic Data Systems
- Electronic Instrument
- Electronic Signs
- Electronics Agents
- Electronics Stocks
- Financial Field
- Generators
- Insulation
- Keypad & Keyboard
- Laser
- Lighting Accessories
- Lighting Bulbs & Tubes
- Lighting Fixtures
- Motors & Engines
- Others
- PCB & PCBA
- Power Accessories
- Power Supplies
- Professional Audio, Video & Lighting
- Radio & TV Equipment
- Rectifiers
- Relays
- Semiconductors
- Sensors
- Speaker
- Switches
- Transformers
- Wires, Cables, Cable Assemblies
-
- Energy
- Environment
- Excess Inventory
- Food & Beverage
-
- Alcohol
- Aquatic Products
- Bean Products
- Beverage Processing Machinery
- Beverages
- Bread & Biscuit
- Canned Food
- Cooking Equipment
- Dairy Products
- Egg Products
- Fast-Food
- Food Agents
- Food Ingredients
- Food Processing Machinery
- Food Stocks
- Frozen & Dried Fruit
- Frozen Food
- Honey Products
- Meat & Poultry
- Noodles
- Others
- Snacks
- Tea
-
- Gifts & Crafts
-
- Antique Imitation Crafts
- Antiques & Collectibles
- Artificial Crafts
- Bamboo & Wooden Crafts
- Basketry
- Candles & Holders
- Carving Crafts
- Clay Figurine
- Crafts Gifts
- Crystal
- Folk Crafts
- Gifts & Crafts Agents
- Gifts & Crafts Stocks
- Glassware
- Holiday Gift & Decoration
- Incense & Incensory
- Jade Crafts
- Key Chain
- Metal Crafts
- Natural Crafts
- Others
- Paintings & Calligraphies
- Paints Crafts
- Paper Crafts
- Photo & Picture Frame
- Photo Album
- Plastic Crafts
- Pottery & Enamel
- Promotion Gifts
- Pyrography
- Religious Crafts
- Resinic Crafts
- Sculptures
- Vases
-
- Health & Beauty
-
- Beauty Products Agents
- Bio-technology Products
- Disabilities
- Enzyme (Ferment) Preparations
- Health Product Agents
- Massager
- Medical Equipment
- Medical Implements
- Medical Supplies
- Medicine & Health Products
- Others
- Personal Care
- Pharmaceutic Machinery
- Pharmaceutical Chemicals
- Pharmacy Stocks
- Sex Products
- Veterinary Medicine
- Weight Loss
-
- Home Appliances
-
- Air Purifier
- Air-conditioner
- Audio & Video Equipment
- Blank Records & Tapes
- Dehumidifier
- Fan
- Hair Dryer
- Hand Dryer
- Heaters
- Home Appliances Agents
- Home Appliances Stocks
- Humidifier
- Iron
- Kitchen Appliances
- Others
- Oxygen Setup
- Parts & Accessories
- Refrigerator & Freezer
- Remote Control
- Timer
- Vacuum Cleaner
- Washing Machine
- Water Dispenser
- Water Heater
- Water Softener, Purifier
-
- Home Supplies
-
- Bags & Cases
- Bath & Toilet
- Clocks
- Daily Products Machinery
- Eyewear
- For Babies
- Furniture
- Garden Supplies
- Home Storage & Organization
- Home Supplies Agents
- Home Supplies Stocks
- Household & Sanitary Paper
- Household Plastic Product
- Household Utensils
- Jewelry & Imitation
- Kitchenware
- Laundry Products
- Mirror
- Lighters & Smoking
- Needlework
- Others
- Pest Control
- Tableware
- Umbrella & Raincoats
- Watches
- Window Covering & Decoration
-
- Industrial Supplies
-
- Air Treatment & Conditioning
- Air-Compressing & Air-Separation
- Bearings
- Boilers
- Chains
- Draught Fan
- Energy Saving
- Fasteners
- Filters
- Gaskets & Seals
- Hardware & Tools
- Industrial Materials
- Industrial Supplies Agents
- Industrial Supplies Stocks
- Industrial Washing Machine
- Internal-Combustion Engine
- Materials Handling
- Measurement & Meter
- Metallic Processing Machinery
- Mould
- Others
- Plastic Machinery
- Power Transmission Equipment
- Precision Parts
- Pumps & Vacuum Equipment
- Refrigeration & Heat Exchange
- Spring
- Used Machinery
- Valves
- Welding & Solders
- Woodworking
-
- Minerals, Metals & Materials
-
- Cast & Forged
- Ferroalloy & Products
- Ingot
- Iron & Steel
- Magnetic Materials
- Metal Mineral
- Metal Processing Service
- Metal Stocks
- Metallurgy Machinery
- Metallurgy Supplies
- Mineral & Metals Agents
- Mining Machinery
- New Materials
- Non-ferrous Metal
- Non-ferrous Metal Alloy
- Non-ferrous Metal Products
- Non-metallic Mineral Deposit
- Non-metallic Mineral Products
- Others
- Rare Earth & Products
- Wire Mesh
-
- Office Supplies
- Packaging & Paper
- Printing & Publishing
- Security & Protection
- Sports & Entertainment
- Telecommunications
- Textiles & Leather Products
-
- Bedding
- Chemical Fabrics
- Cotton Fabrics
- Denim & Jean Fabric
- Embroidery & Crafts Textile
- Feather & Down Raw Materials
- Fur Raw Materials
- Grey Fabrics
- Household Textile Product
- Industrial Fabrics
- Interweave Fabric
- Knitting Fabrics
- Leather Products
- Linen/Ramie/Hemp
- Non-woven Cloth
- Others
- Silk
- Textile Accessories
- Textile Agents
- Textile Machinery & Parts
- Textile Materials
- Textile Processing
- Textile Stocks
- Thread
- Wool Fabrics
- Yarn
-
- Toys
- Transportation